Does it Pay to Calibrate? Collecting Quality Yield Data.
- Rachel
- Aug 28, 2018
- 5 min read
Updated: Aug 30, 2018
It’s the time of year we need to start thinking about yield data quality. We hear this every year: “make sure to calibrate your yield monitor!” But why should we do it? Does it really matter? And what is the best method for calibration? Often time when we get into the thick of harvest, it seems hard to take the time to stop and calibrate correctly. So how essential is the calibration processes?

Bob Nielsen from Purdue University reminds: “Garbage in, garbage out.” If we are wanting to use our yield data for any useful purpose, it is essential that we collect good data to begin with. When we are using our yield data as part of variable rate fertilizing, variable rate seeding, hybrid comparisons, topographic response, or management zone creation, poor quality yield data will result in poor outcomes for all of those subsequent management practices. So the question boils down to: do you want to make use of your yield data? If so, take the time to calibrate!
Let’s think of the yield monitoring system as a whole. It is much more than just a monitor mounted in the cab. It includes parts like the clean grain elevator, the mass flow sensor, the moisture sensor, as well as fixed settings such as lag time and header width. Of these, the mass flow sensor is the most important. Located at the top of the clean grain elevator is an impact plate. Grain is carried to the top of the clean grain elevator where it is thrown against the sensor. The mass flow sensor reads this voltage and then converts this to a specific flow rate in pounds per second. The amount of grain flowing through the system is what we are trying to correlate.
Mass Flow Sensor
Some manufacturers will call for a one point correlation of the mass flow sensor, and some for a multi-point. We would recommend a multi-point calibration to get your system as fine tuned as possible. It is recommended that you calibrate somewhere between 3 and 6 times. Why so many? Simply doing a two point calibration will give us a linear response. The results we get from the mass flow sensor are non-linear. They are curved. By adding in a third, fourth, or fifth calibration load, we are able to fit our correlation more closely to that non-linear mass flow response. This will reduce the error from the mass flow estimates. We can see the value of multi-point calibration in Figure 1. With only a two point calibration at a low flow and high flow value, the linear relationship will overestimate the actual mass flow. In scenario B, a multi-point calibration reduces error and more closely represents the actual mass flow values.
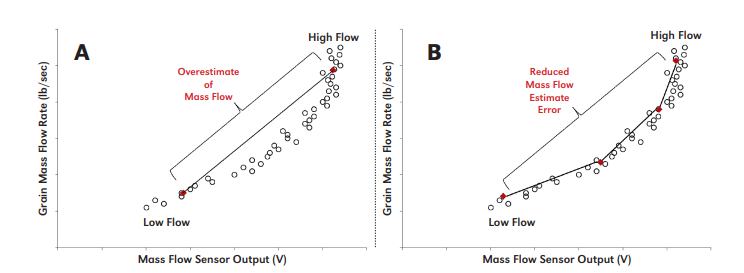
To appropriately correlate the mass flow sensor, values across a wide range of mass flows must be collected. This can be achieved by varying the harvest speeds. Harvest one calibration load at a “slow” speed, one at an “average” speed, and another at a “faster” speed. Each of these different calibration loads should occur at a uniform flow rate. This will all be relative to what you consider slow or fast, but try to provide enough variation in speed to give a wide range of mass flows. The other option for providing a range of mass flow values is to vary the number of rows harvested. Complete one calibration with a quarter of the head, then half, then three quarter, and then a full header width. Try to complete these calibrations in a portion of the field known to be fairly uniform. Collect between 3000 – 10,000 pounds of grain. Weigh this amount with a certified weigh wagon certified scale. Using the calibration method described in your manual, adjust the monitor value to the actual certified value from the weigh wagon or scale. Again, repeat this process multiple times for a best fit curve of our mass flow. Our ultimate goal with mass flow calibration is to measure a sample of all yield levels or flow rates you would likely come across during harvest. It is also advised after testing moisture that separate mass flow calibrations are completed for above and below 20% moisture to account for the differences in grain weight and movement.
Moisture Sensor
Similar to the mass flow sensor, the moisture sensor should also be calibrated for accuracy. This in fact should be calibrated each time you calibrate the mass flow sensor as moisture readings can effect how mass flow is interpreted. Moisture should also be recalibrated several times throughout the year to compensate for changing crop conditions. Harvest a between 3000 and 10,000 pounds of grain. Randomly pull samples and test with a portable moisture tester, or take a sample to an elevator for a precise reading.
Sources of Error
There are several other factors that can contribute to faulty or inaccurate readings. Lag time, or the time it takes from grain to move from the head through to the mass flow sensor needs to be recorded to correctly position grain readings at the spot they were collected.
Verify that header size is correctly recorded in the monitor. If this value is incorrect, this can underestimate or overestimate yield. Even if this is set correctly, header width can still contribute to errors, particularly in cases where automatic header width is not available. The automatic header width value is calculated based on portions of the field covered. If automatic header width is not available for your system, the combine will assume a full header width even on areas of the field such as point rows or angled passes into headlands.
This can contribute to low yield estimates in those areas.
Additionally, if the head is left down during turns or covering parts of the field with harvested crop, low or zero recordings will be recorded and affect the field average. This also logs more acres than are actually harvested, further contributing to lower field totals.
Moving Through the Harvest Season
It will be important to calibrate the yield monitor system again as harvest progresses. When initially calibrating the system, we will likely be calibrating on higher moisture grain. This flows and performs very different than grain that is 5 percentage points lower later in the harvest season. As crop conditions change, take note and calibrate accordingly. Errors of 7-10% can result from only calibrating at the beginning of harvest. Additionally, a host of factors can affect the accuracy of calibration. Mass flows outside of the calibrated range, changes in moisture content, changes in test weight or grain shape, or differences in hybrids all contribute to seasonal changes. It is important to calibrate again mid season to account for some of these issues.
Data to Decisions
Yield data is one of the major base layers for a lot of decisions we make prepping for the next growing season. Ensuring that data is recorded accurately is vital for generating new data layers and making decisions based on them. Collecting good data gets us one step closer to useful management decisions.
Advances are being made with new technologies to record and verify yield data. A new system from John Deere called Active Yield uses weigh pads in the grain tank for on the go calibration of the mass flow sensor. Technologies like these will drastically reduce time for yield calibration and help producers collect high quality data with ease.
How to Calibrate YOUR Yield Monitor
This link provides some visual guides to step through how to calibrate yield monitors for some of the more common setups. First select your operation and brand, then specific monitor and objective. Then follow the steps provided to calibrate.
And as always, your combine or monitor manual is a great resource for completing yield monitor calibrations.
Resources
Comments